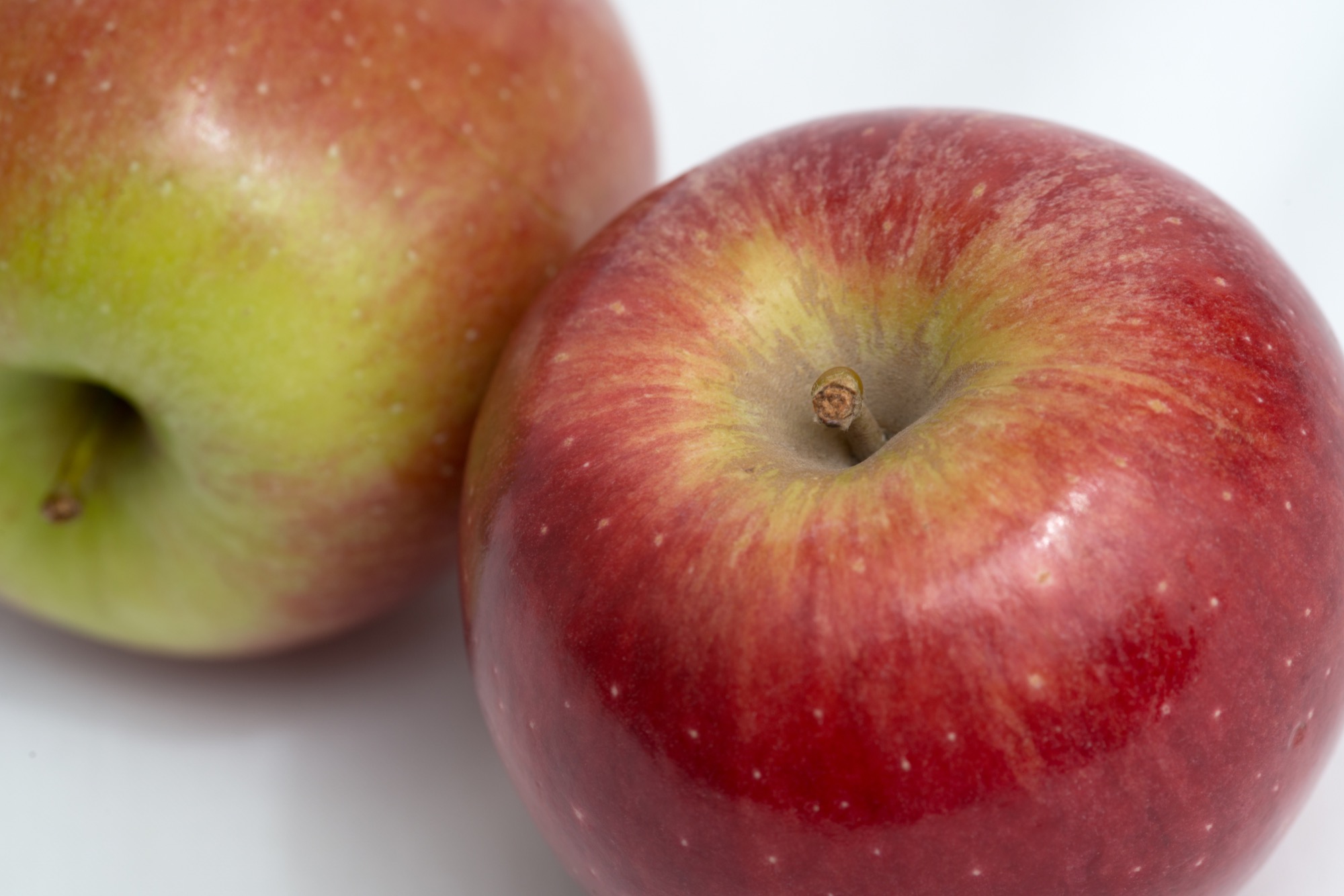
We are proud to share the remarkable story of Ko Oostdijk. Ko is a well-known figure in the fruit and vegetable sector, especially for his vast knowledge and passion. At The Greenery, Ko has done a lot as the regional hard fruit controller. As the first inspector at The Greenery, Ko started conducting quality inspections with QC One, showing how important quality and innovation are to him. Ko and Stefan look back on Ko’s long career together.
Before QC One came along, Ko Oostdijk was already making inspection reports standard using Excel. “I made the first standard reports with Excel, but QC One took them to a new level,” Ko says. This change made it possible to make reports that were not just standard but also clear and easy for everyone to understand. Thanks to Ko’s ideas and using this new technology, the inspection reports now match what customers want exactly: clarity and consistency for each product. “Moving forward naturally,” says Ko, whose method has helped make quality checking at The Greenery more efficient and open.
Ko Oostdijk knows much more than just the technical stuff. He can ‘taste’ with his eyes. “By just looking, you learn a lot; the colour, texture, how and where it grows, and the best time to pick it tells me if an apple will taste sweet, sour, juicy, or dry,” Ko explains. This special skill, important at The Greenery, is highly valued. He was also the first one to use QC One on an iPad. “A whole load was quickly done in QC One on a Friday afternoon, and by 3:30 p.m., I was finished. No mess with notes on paper, but everything tidy in the app. Finishing and driving away felt great,” he shares. In a cold store, Ko found that even without internet, his way of using QC One still worked. “I checked pears in every cell, without being able to sync. I kept recording and thought, now I’m really testing QC One. At home, all my 75 photos were still there safely. That’s a big plus!” Ko remembers.
Ko Oostdijk knows much more than just the technical stuff. He can ‘taste’ with his eyes. “By just looking, you learn a lot; the colour, texture, how and where it grows, and the best time to pick it tells me if an apple will taste sweet, sour, juicy, or dry,” Ko explains. This special skill, important at The Greenery, is highly valued. He was also the first one to use QC One on an iPad. “A whole load was quickly done in QC One on a Friday afternoon, and by 3:30 p.m., I was finished. No mess with notes on paper, but everything tidy in the app. Finishing and driving away felt great,” he shares. In a cold store, Ko found that even without internet, his way of using QC One still worked. “I checked pears in every cell, without being able to sync. I kept recording and thought, now I’m really testing QC One. At home, all my 75 photos were still there safely. That’s a big plus!” Ko remembers.
Knowing what’s wrong with a product is important to Ko. “I’s good to know what kind of damage there is and why it happens,” Ko says. “This way, you can advise the grower on what he can improve in his process.” The quality is much higher today than it used to be. “Apples that used to be sold as class 1 are now just good enough for applesauce.” With QC One, you can directly inspect for the right quality. “By customizing QC One according to your own insight, you can make optimal use of it during a control.” Stefan says with a laugh: “You’re just a good guy, Ko!”
A situation with an English supplier where his eye for detail and knowledge were crucial, remains with him. “We faced a big challenge when a batch of fruit did not meet expectations. Thanks to QC One, I was able to present detailed reports and analyses that not only pointed out the cause of the problem but also how the customer could prevent this in the future,” Ko tells. By doing good research and a lot of product knowledge, the customer’s trust was regained. This shows how good knowledge and the technology of QC One work hand in hand.
Ko’s role goes beyond his work; he is also a mentor. “The best thing about this job? Every day is different, and you work with living products,” says Ko. Stefan agrees: “Ko’s dedication will continue to contribute to our mission to revolutionize quality control within the sector.” Now that Ko is retiring, he looks forward to sharing his knowledge with QC One over a good cup of coffee and a Zeeland bolus now and then. “My heart will always be with the fruit and vegetable sector,” says Ko. Stefan adds: “We are grateful for Ko’s efforts. His experiences are invaluable.” Reflecting on Ko’s contribution, Stefan says: “What Ko teaches us is that true expertise lies in the hearts and souls of those who dedicate their lives to their craft.” Ko’s story is a source of inspiration and proof of the power of passion, experience, and sharing knowledge.