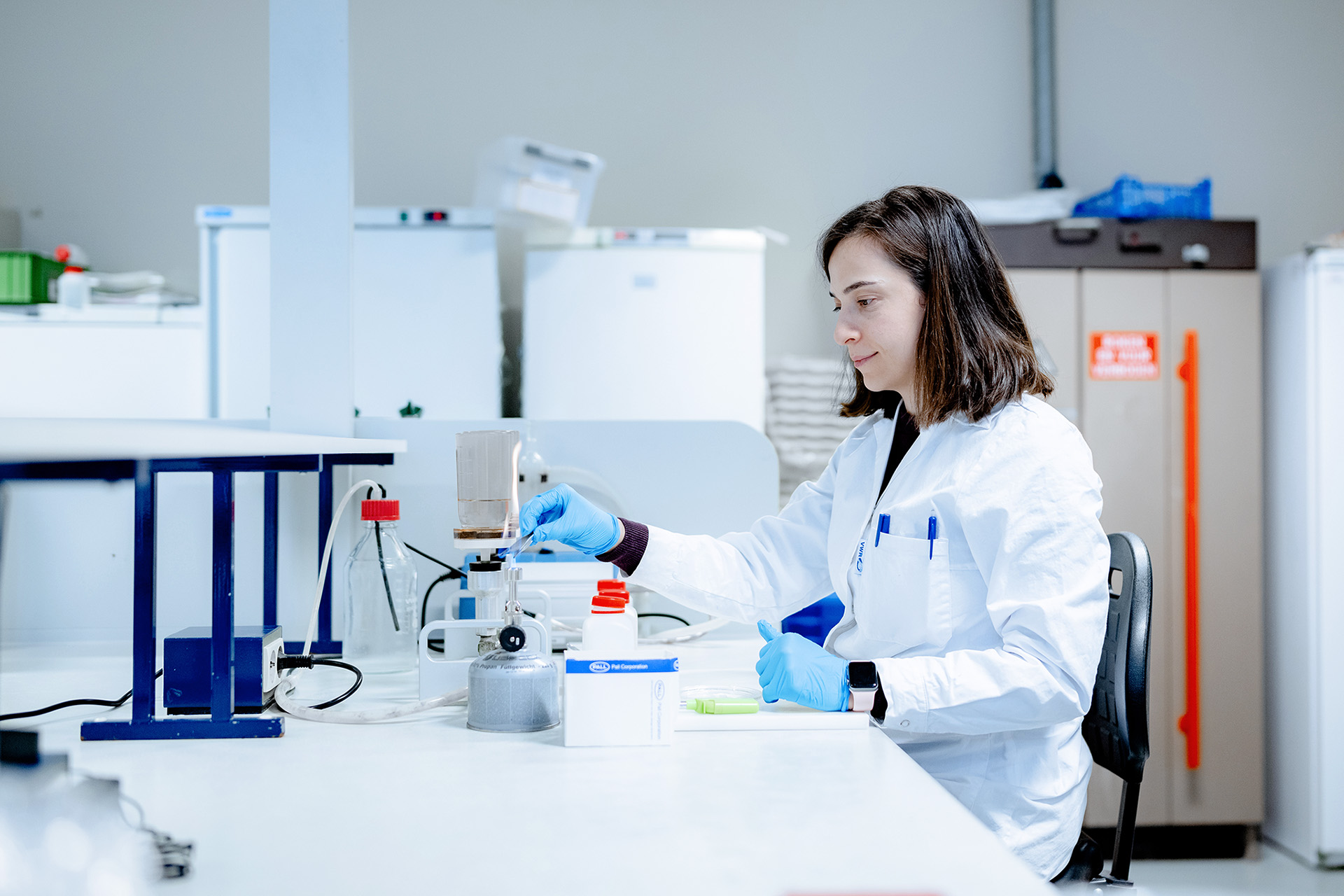
We investigate the quality of your product
Accredited laboratories that perform various analyzes under the scope of the accreditation
Our QA advisors provide support with QA activities
Online QA and QC Software for better and more efficient quality assurance
Own team of certified auditors and recognized inspectors
We check your labels and ensure that specification management is in order
Normec Foodcare offers a proven total solution in the field of quality and industrial food safety in the food industry. We take care of complete projects in the field of process control for quality and food safety, laboratory research, taste tests, QA automation, flexible use of quality managers, education and training, risk management and label control.